Understanding PBR vs KBR: Key Differences Explained
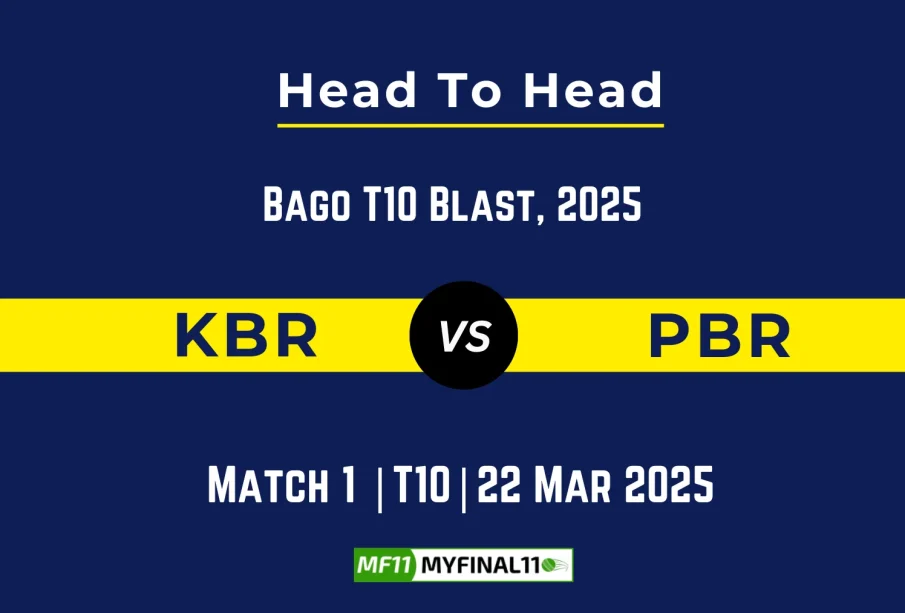
Introduction
The dynamic fields of chemical engineering and materials science often find themselves discussing various compounds and methodologies. Among these, Polybutadiene Rubber (PBR) and Kraton Block Rubber (KBR) are two significant materials that engineers and manufacturers commonly employ. Understanding the differences between PBR and KBR is essential for professionals working in industries such as automotive, sealants, and adhesives, where the choice of material can affect the performance and durability of products.
What is PBR?
Polybutadiene Rubber (PBR) is a synthetic rubber produced from the polymerization of butadiene. It is known for its excellent abrasion resistance, low rolling resistance, and high resilience, making it suitable for applications such as tires, mats, and wires. PBR is primarily utilized in the automotive industry, where its resilience and durability are critical.
What is KBR?
Kraton Block Rubber (KBR), on the other hand, is a thermoplastic elastomer made from styrene and butadiene. KBR provides excellent elasticity, clarity, and chemical resistance, which make it ideal for applications requiring flexibility and durability. Its applications include adhesives, coatings, and a variety of consumer products where a balance of toughness and stretchability is essential.
Key Differences
1. **Composition**: One of the main differences between PBR and KBR lies in their chemical composition. PBR is a homopolymer made from butadiene, while KBR is a block copolymer that includes both styrene and butadiene components. This difference significantly influences their properties and performance in applications.
2. **Mechanical Properties**: PBR typically exhibits better abrasion resistance compared to KBR, making it advantageous in applications involving heavy wear and tear, such as tires. However, KBR often surpasses PBR in terms of flexibility and elasticity, contributing to its widespread use in applications calling for bending and stretching.
3. **Processing**: The processing methods for PBR and KBR can also differ significantly. PBR can be processed similarly to traditional thermoplastics, while KBR often requires specialized processing techniques to achieve the desired material properties. This can impact production timelines and costs.
Conclusion
In conclusion, choosing between PBR and KBR significantly depends on the specific requirements of the application and the desired properties of the final product. Understanding the nuances of each material helps engineers make informed decisions that enhance product performance and durability. As industries continue to evolve and innovate, the importance of recognizing the differences between materials like PBR and KBR will only become more critical for future advancements in manufacturing and material science.